目前,对保护环境和节约能源的呼声高涨,使得国内的新能源电动汽车倍受关注。大功率封装器件在调控汽车速度和储存-转换交流和直流上发挥着决定性作用。而高频率的热循环对电子封装的散热提出了严格的要求,同时工作环境的复杂性和多元性需要封装材料具有较好的抗热震性和高强度来起到支撑作用。此外,随着以高电压、大电流和高频化为主要特征的现代电力电子技术的高速发展,应用于该技术的功率模块散热效率更成为了关键。电子封装系统中的陶瓷基板材料是高效散热的关键,同时为了应对工作环境的复杂化也应具有高强度和高可靠性。
近年来已经大规模生产、应用较为广泛的陶瓷基板主要有:Al2O3、BeO、SiC、Si3N4、AlN等。
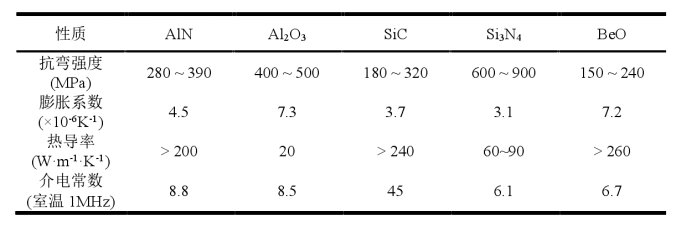
不同种类陶瓷基板的性能(来源:廖圣俊.基片用氮化硅陶瓷材料的制备及性能研究)
Al2O3由于其制备工艺简单、绝缘性好,且耐高温,目前在散热基板行业中占有重要的地位。但是Al2O3的热导率较低,无法满足高功率大电压器件发展要求,只适用于对散热要求较低的工作环境,而且由于弯曲强度较低也限制了Al2O3陶瓷作为散热基板的应用范围。
BeO陶瓷基板虽然具有较高的热导率和较低的介电常数,满足高效散热的要求,但是由于其具有毒性,对工作人员的健康产生影响,不利于大规模应用。
AlN陶瓷具有较高的热导率,被认为是散热基板的候选材料。但AlN陶瓷抗热震性能差,易潮解,强度韧性较低,不利于在复杂的环境中工作,难以保证其应用的可靠性。
SiC陶瓷虽然具有很高的热导率,但是由于其具有较高的介电损耗和较低的击穿电压,不利于应用在高频高压的工作环境中。
氮化硅是国内外公认兼具高导热、高可靠性等综合性能最好的陶瓷基板材料。尽管Si3N4陶瓷基板具有略低于AlN的导热性,但其抗弯强度、断裂韧性都可达到AlN的2倍以上;同时,Si3N4陶瓷的热导率远大于Al2O3陶瓷;此外,Si3N4陶瓷基板的热膨胀系数与第3代半导体衬底SiC晶体接近,使其能够与SiC晶体材料匹配性更稳定。这使Si3N4成为第3代SiC半导体功率器件高导热基板材料的首选。
本篇,小编就盘点一下Si3N4陶瓷基板在新能源汽车上面的那些应用。
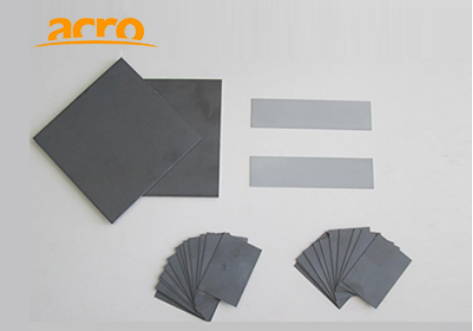
氮化硅导热基板(来源:埃克诺新材料(大连)有限公司)
Si IGBT
IGBT是新能源汽车电机控制系统的核心器件,约占电机驱动系统成本的一半,而电机驱动系统占整车成本的15-20%,也就是说IGBT占整车成本的7-10%,是除电池之外成本第二高的元件,IGBT的质量很大一部分也决定了整车的能源效率。
IGBT投入市场这么多年以来,其自身的潜力已经挖掘的差不多了,大家都把精力转移到IGBT的封装上,也就是散热。车用IGBT的散热效率要求比工业级要高得多,逆变器内温度极高,同时还要考虑强振动条件,车规级的IGBT远在工业级之上。电动汽车用IGBT模块的功率导电端子需要承载数百安培的大电流,对电导率和热导率有较高的要求,车载环境中还要承受一定的振动和冲击力,机械强度要求高。
对于车用IGBT,氮化硅是再适合不过的。氮化硅陶瓷电路板可以适应高温高压的工作环境。能及时散去电源系统中的高热量,能适应汽车内部恶劣的环境,各大功率负载的正常运行的同时,保护芯片正常工作。延长电子设备的使用周期。节约更多空间,为新能源汽车提供更多可能性。
SiC MOSFET
在新能源汽车的核心电机驱动中,采用SiC MOSFET器件比传统Si IGBT带来5%~10%续航提升,未来将会逐步取代Si IGBT。但SiC
MOSFET芯片面积小,对散热要求高,氮化硅陶瓷基板具备优异的散热能力和高可靠性,几乎成为SiC MOSFET在新能源汽车领域主驱应用的必选项。
目前已经量产的Tesla model 3已经大批量使用氮化硅陶瓷基板,应对SiC MOSFET器件散热。
比亚迪e3.0平台推出的全新一代SiC电控,采用了自主研发的全新SiC
MOSFET电机控制模块、高性能氮化硅陶瓷以及集成NTC传感器,使整个电控单元功率密度提升近30%,电流最大支持840A,电压最大1200V,电控最高效率达99.7%。
(素材来自网络,侵删)