碳化硅是 C—Si
共价键相结合的一种化合物,具有良好的耐磨性和抗热震性,以及耐腐蚀性强,热导率高等优良性能,被广泛用于航空航天、机械制造、石油化工、金属冶炼以及电子行业,特别用于制作耐磨损部件和高温结构部件。反应烧结碳化硅陶瓷是最早实现工业化生产的结构陶瓷之一。传统反应烧结碳化硅陶瓷是以碳化硅粉和少量炭粉为原料,
经高温渗硅反应烧结而成,烧结时间长,温度高,能耗大,成本高。随着反应烧结碳化硅技术的广泛应用,传统反应烧结碳化硅陶瓷满足不了工业上对碳化硅陶瓷形状复杂性的要求。
近年来,部分采用碳化硅纳米粉制备出烧结密度高,抗弯强度大的碳化硅陶瓷,极大提高了材料的力学性能。但碳化硅纳米粉原料售价每吨在万元以上,生产成本过高,不利于规模化推广。在本工作中,以来源广泛的木质炭粉为碳源,微米碳化硅为骨料,采用注浆成型技术制备反应烧结碳化硅陶瓷素坯。这既可以免除碳化硅粉的预合成,降低碳化硅陶瓷的制备成本,又可制备大尺寸,形状复杂的薄壁制品,为反应烧结碳化硅陶瓷的性能改善及应用提供一定的参考。
试验
1.原料
试验原料有: d50 = 3.6μm 的碳化硅,w(SiC)≥98% ; d50 = 0.5μm 的炭黑,w(C)≥99% ; d50 = 10μm
的石墨,w(C)≥99% ; 分散剂为聚乙烯吡咯烷酮 K30( K 值为 27 ~ 33 )和 K90( K 值为 88 ~ 96 ) ; 减水剂聚羧酸
CE-64,脱模剂 AO,去离子水。
2.试样制备
试验按表 1 配料,用电动搅拌器搅拌 4 h,得到混合均匀的浆料。保持浆料黏度≤1000 mPa·s,将混合浆料倒入准备好的石膏模具中浇注成型,静置
2 ~ 3 min 通过石膏模具脱水得到坯料。在阴凉处放置 48 h后,将坯料从石膏模具中取出得到生坯,放置在真空干燥箱内于 80 ℃ 烘干 4 ~ 6
h,然后在马弗炉内 800 ℃脱胶 2 h 得到素坯。选用炭黑、硅粉、氮化硼的质量比为 1∶ 100∶ 2000 的混合粉作为包埋粉对素坯进行包埋,在 1720
℃ 的烧结炉中烧结 2 h,烧结完成后得到全细粉碳化硅陶瓷。
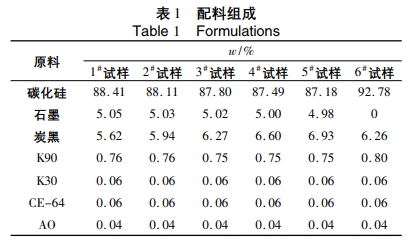
3.性能检测
采用旋转黏度计测量室温下不同搅拌时间( 1 ~ 5 h ) 的浆料黏度,根据国标 GB /T 25995—2010 测量试样素坯的体积密度,按 GB
/T 6569—2006 检 测 1720 ℃ 烧后试样的抗弯强度,试样大小为 3 mm × 4 mm × 36 mm,跨距为 30 mm,加载速度为 0.5
mm·min-1。用 XRD 和 SEM 分析 1720 ℃ 烧后试样的物相组成和微观结构。
结果与讨论
1.物理性能
1.1搅拌时间对浆料黏度、素坯体积密度和显气孔率的影响
图 1、图 2 分别示出了 2# 试样搅拌时间与浆料黏度的关系及搅拌时间与素坯体积密度和显气孔率的关系。
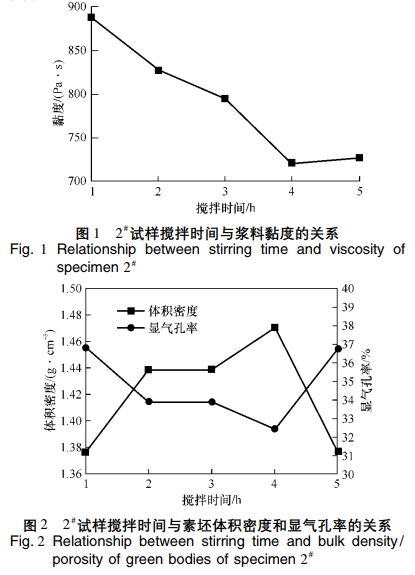
由图 1 可见,随着搅拌时间的增加,黏度下降, 4 h 时浆料黏度达到最低为 721 mPa·s,然后趋于平缓。图 2 表明,2#
试样素坯的体积密度最大为 1.47 g·cm-3,显气孔率最低为 32.4%
。黏度越低则分散性越好,浆料分散得越均匀,越有利于提高碳化硅陶瓷的性能。因此,制备全细粉碳化硅陶瓷所用的浆料黏度相对较低。由于搅拌时间不足会导致碳化硅细粉混合不均匀,搅拌时间过长会蒸发较多水分导致体系不稳定,不利于制备性能优良的全细粉碳化硅陶瓷材料。综上,混合浆料的最佳搅拌时间为
4 h。
1.2石墨对浆料黏度、素坯体积密度和显气孔率的影响
表 2 列出了添加石墨的 2# 试样与未加的 6# 试样浆料黏度、素坯体积密度和显气孔率。可以看出:
添加石墨后浆料黏度降低,素坯体积密度增加,显气孔率减小。由于石墨具有润滑作用,降低浆料黏度,使得所制浆料分散均匀,增加全细粉碳化硅陶瓷的致密度。未添加石墨的浆料黏度大,分散性和稳定性差。因此,制备全细粉碳化硅陶瓷材料添加石墨是必要的。

1.3炭黑含量对素坯体积密度和显气孔率的影响
图 3 示出了不同炭黑添加量试样素坯的体积密度和显气孔率。由图 3 可知,2# 试样素坯的体积密度最大,为 1.47 g·cm-3 ;
素坯显气孔率较小,为 32.4%。但显气孔率不可太小,否则不易渗硅。
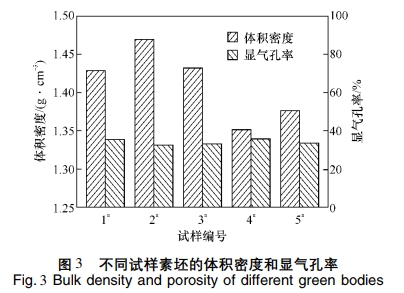
2.物相组成
图 4 为 2# 试样素坯、经过 1720 ℃ 烧后试样的XRD图谱。从图中可知,2# 试样素坯中含有石墨、β-SiC,烧后的试样中含有
Si、β-SiC 以及 α-SiC。这是由于高温烧后试样中有部分 β-SiC 转化成了 α-SiC。由图中还可知,高温渗硅反应烧后的试样中多了Si组分,少了 C
组分。其原因是素坯用含 Si 粉的包埋, 进行高温渗硅,实现反应烧结时 Si 与 C 反应生成 SiC 并填充了孔隙。
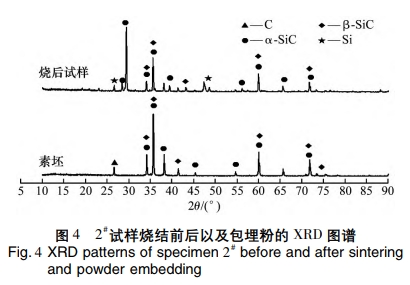
3.显微结构
3.1不同试样素坯的断口形貌
图 5 所示为不同试样素坯的断口形貌。从图 5 可以观察到有细碳化硅、石墨以及孔隙; 其中,1# 、4# 、 5#
试样中直径大的片状物相对较多,孔隙多且分布不 均匀,即颗粒大小分布不均匀,可能是制备浆料时混 合不均匀导致分散不均匀,体系不稳定,进而制得的
素坯致密度较小,气孔率较大。从微观形貌显示炭黑的最佳添加量为 5.94% (w) ,即 2#试样。
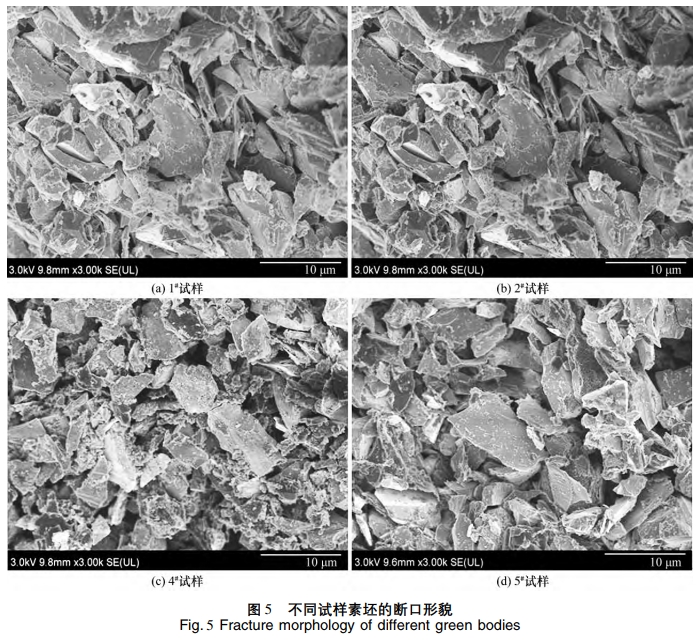
3.2 2# 试样烧后的断口形貌
图 6 为 2# 试样经 1720 ℃ 烧后的断口形貌。可以看出: 碳化硅颗粒紧密分布且较为均匀,基本无孔隙存在;
碳化硅颗粒呈现长大趋势,这是由于高温作用造成的晶粒长大。图中还显示,有部分较小的碳化硅颗粒分布在原有的骨架碳化硅颗粒之间,这是 反应烧结新生成的
SiC。同时还有部分残余 Si,这是素坯当中的空隙在烧结之后 Si 蒸气冷却后凝固残留的。这进一步验证了XRD测定的结果。残余 Si
的存在能填补原有的孔隙,减少应力集中现象。但由于 Si 的熔点较低,会影响制品的高温使用性能。烧后制品体积密度为 3.02 g·cm-3,抗弯强度达到了580
MPa,比普通反应烧结碳化硅强度提高了一倍以上。

结论
(1) 制备全细粉碳化硅陶瓷所用浆料的最佳搅拌时间为 4
h。添加石墨后浆料黏度降低,素坯体积密度增加,显气孔率减小,增加了全细粉碳化硅陶瓷的致密度。
(2) 制备全细粉碳化硅陶瓷时,炭黑的最佳添加量为 5.94% (w) 。
(3) 烧后碳化硅颗粒紧密分布且较为均匀,基本无孔隙存在; 碳化硅颗粒呈现长大趋势,烧后制品密度为 3.02 g·cm-3 ,抗弯强度为 580
MPa,全细粉制备的碳化硅陶瓷在力学强度和致密度上有较大提高。
(素材来自网络,侵删)