1 引言
所示防护壳体是某环保设备的零件之一,材料为不锈钢 SUS304L,生产批量较大。装配后,制件外落在设备上,故要求其表面质量较为严格,拉伸后要求制件表面划伤、划痕不超过 0.10mm。该制件成形采用落料、3次拉伸工序。
2 拉伸模材料的选择
2.1 金属薄板拉伸对模具材料的要求
(1)较高的硬度,良好的耐磨性。
(2)良好的抗粘附性。
(3)良好的热处理性能(淬硬性、淬透性、微变形等)。
(4)一定的韧性。
(5)良好的机械加工性能。
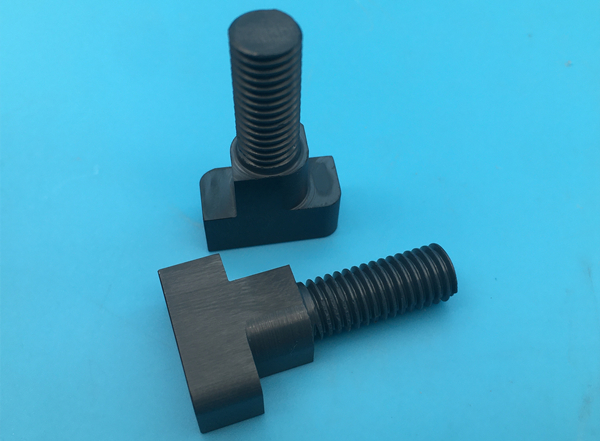
2.2 黑色金属拉伸对模具材料的选择原则
模具材料的选择原则:
不同材料的模具,热处理、表面状态不同、与被加工材料的亲和性、抗高温摩擦粘结的程度也不同。因此,需要根据拉伸材料的性质、表面质量要求、生产批量等因素,恰当、经济地选择模具材料。通常拉伸硬材料时使用软质模具材料,而加工软质材料,应使用硬质模具材料。
2.3 防护壳体拉伸模材料的选择
将各次拉伸凹模材料都选用冷作模具钢(如Cr12MoV、Cr12等),热处理后进行氮化处理。在实际生产中,第一次拉伸20件左右,制件表面出现明显的划伤,不得不去抛光模具。由于经常抛光凹模,制件尺寸超差,致使模具报废,一度使生产无法进行。由于该制件批量较大,为保证模具具有较高的使用寿命,同时为避免毛坯制件表面划伤、划痕等缺陷,各次拉伸凹模选用硬质合金材料。使用硬质合金组合凹模后,尽管各次拉伸凹模的使用寿命得到一定程度的提高,但毛坯制件表面也经常出现划伤、划痕等缺陷,需要抛光模具。由于硬质合金材料硬度较高,抛光比较困难。
3 模具产生划伤的原因及解决措施
3.1 模具产生划伤的原因
不锈钢板材在拉伸成形过程中,材料在变形流动过程中要产生很大的抗力,即使模具表面粗糙度很低,工件与模具之间必然要产生摩擦力。由于不锈钢材料与模具材料具有一定的粘合性,加剧了工件与模具表面的相互摩擦。另外,不锈钢板材在拉伸成形过程中,由于其内部金属晶格要发生错移和形变,加之不锈钢与金属模具存在亲和性,将产生大量的热能,工件与模具接触部位由于瞬间高温而出现冷焊粘接现象,高温冷焊粘接,导致工件因表面划伤严重,质量无法保证,尽管硬质合金硬度较高,需要经常抛光模具。
3.2 解决措施
反应烧结的氮化硅陶瓷材料具有以下特点:
a.耐磨性高。氮化硅陶瓷材料耐磨性很高,可以保证拉伸模在工件允许的变形程度内,都能长期工作,并保证拉伸件尺寸不变。
b.抛光性能优良。氮化硅陶瓷材料具有良好的抛光性,能加工成镜面状态的模孔,保证拉伸金属制件表面的高质量。
c.对拉伸金属的粘附性小。氮化硅陶瓷为无机非金属材料,与金属材料不存在亲和性,避免了因粘着磨损引起的工件表面划伤。
d.氮化硅材料硬度高。硬度可达1600HV以上。
e.摩擦系数小。当模具表面精加工到 0.005~ 0.025mm时,摩擦系数小到0.01,摩擦系数小,能量消耗比采用钢模降低60%以上。
f.耐腐蚀性能好。氮化硅陶瓷材料为无机非金属材料,对冷却润滑剂具有良好的耐腐蚀性。
g.热膨胀系数接近于钢。
h.氮化硅陶瓷材料抗压强度虽然很高,但脆性较高,易于断裂,为防止氮化硅陶瓷模具在拉伸时胀裂,在陶瓷模具外加上预应力模套。以保证陶瓷模具具有较高寿命。
(2)氮化硅陶瓷材料适用性广。
由于氮化硅陶瓷材料具有以上特点,氮化硅陶瓷凹模材料可拉伸各种牌号的黑色金属、有色金属材料,尤其适合不锈钢材料的拉伸。
(3)氮化硅陶瓷凹模对拉伸设备的要求。
针对氮化硅陶瓷脆性较高,不能承受较大的冲击力的特点,采用氮化硅陶瓷凹模进行拉伸生产时,一般选用压力平稳、冲击力小的液压机或双动拉伸压力机。
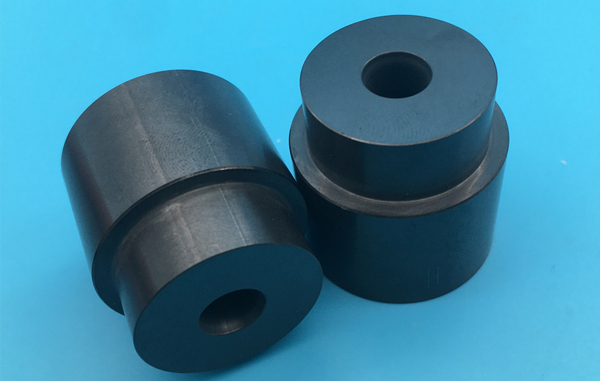
4 拉伸凹模材料改为氮化硅陶瓷
由于氮化硅陶瓷材料具有上述优点,选用氮化硅陶瓷材料制造防护壳体各次拉伸组合凹模,设计的第三次拉伸氮化硅陶瓷组合凹模。

由于我公司无氮化硅陶瓷模具加工能力,该氮化硅陶瓷组合凹模由深圳市海德精密陶瓷有限公司制造。
避免了金属材料与氮化硅陶瓷凹模之间由于瞬间高温而出现冷焊粘接现象,制件表面质量无划伤、划痕等缺陷。同时,摩擦系数较小,减小了拉伸力,降低了拉伸设备的吨位,节省了能源,氮化硅陶瓷组合凹模的使用寿命高与硬质合金组合凹模相当。
5 结束语
通过近多年的实际应用,氮化硅陶瓷材料用于不锈钢板材拉伸成形,显著提高工件的外观质量,模具使用寿命显著提高,比冷作模具钢提高寿命5~10倍,提高了生产效率,降低了生产成本,取得了较好的经济效益和社会效益。